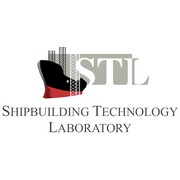
Identity
Establishment details:
Government Gazette 155/18-07-1975
Director:
Professor Nicholas G. Tsouvalis
Tel: +30 21 07721413, +30 21 07722872
Fax: +30 21 07721412
Email: tsouv@mail.ntua.gr
Website: http://users.ntua.gr/tsouv
Contact Info:
Professor Nicholas G. Tsouvalis
NATIONAL TECHNICAL UNIVERSITY OF ATHENS
School of Naval Architecture and Marine Engineering
Shipbuilding Technology Laboratory
Iroon Polytechniou 9, 15780 Zografou, Athens
Tel: +30 21 07721413, +30 21 07722872
Fax: +30 21 07721412
Email: tsouv@mail.ntua.gr
Website:
http://stl.naval.ntua.gr/
The Shipbuilding Technology Laboratory (STL) was founded in 1975 with the aim of conducting research in the area of shipbuilding, technical marine materials, and the study of the processing factors that contribute to the structural behavior of marine structures. This is achieved through processes of education and research, as well as the provision of specialized expertise to the industry. STL has extensive experience in the areas of:
• Structural analysis and optimization of marine structures
• Monitoring of the structural behavior of these structures with machine learning models
• Materials science and technology
• Conventional and non-conventional construction processes
• Welding technology
• Metallurgical characterization, failure analysis of welded and other materials
• Corrosion and materials protection
• Non-destructive testing
• Use of advanced materials (e.g. composite materials) in shipbuilding and other applications
• Technology of bonded joints of metallic and composite materials
• Characterization of such materials through experimental testing
• Design and implementation of full-scale experimental tests for recording the structural response of large constructions.
STL has strong links with several international and European organizations and industries, either in the context of service provision or in joint participation in research projects.
The Shipbuilding Technology Laboratory consists of four units:
• Tests and Measurement Unit
• Microstructure Characterization Unit
• Structural Design and Analysis Unit
• Production Processes Unit
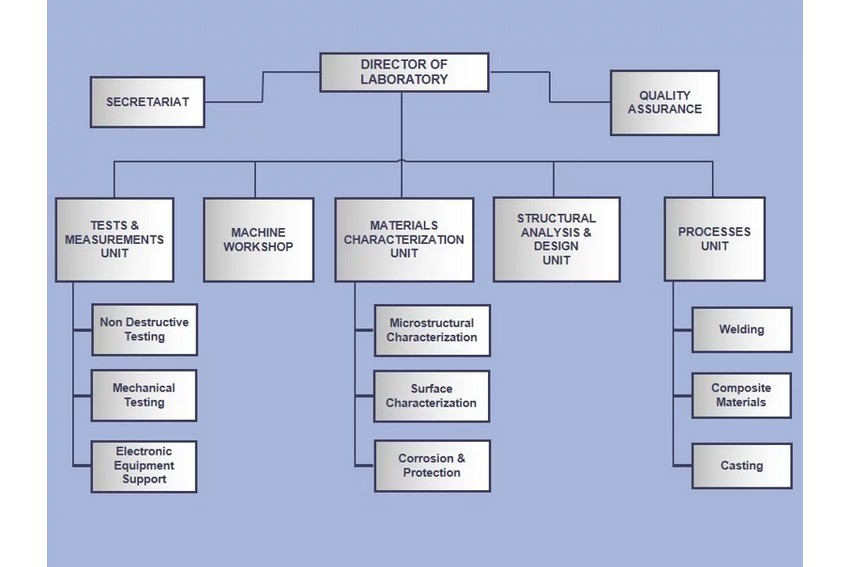
Equipment of STL
• Equipment for determining the mechanical properties of materials (two hydraulic testing machines with a capacity of 250 and 100 kN)
• Equipment for characterizing the physical properties of materials
• Equipment for monitoring and measuring small, medium and full-scale structures (various types of sensors, multichannel data acquisition unit)
• Welding equipment (welding machines for Gas, SMAW, GMAW, GTAW, SAW, Friction Stir Welding, Brazing and Soldering Techniques, and welding robots)
• Basic equipment for manufacturing composite materials (tools, curing furnace, etc.)
• Non-destructive testing equipment (various types of sensors, automated ultrasonic testing system ULTRAPAC II combined with a rotating table, various portable ultrasonic systems: Olympus 38DL-Plus, POCKET UT SYSTEM, BondMaster 1000e+)
• Equipment for characterizing the microstructure of materials (Scanning Electron Microscope, XRF analysis, optical microscope, stereoscope, image processing, macro and micro-hardness testers, and replicas technique)
• Equipment for characterizing surfaces (Tribometer, 3D laser scanner & digitizer, and roughness testers)
• Equipment for characterizing corrosion (Electrochemical cell, potentiometer, special software, salt spray chamber)
• Equipment for thermal and cryogenic processes (Furnaces, Cryogenic processor)
• Casting equipment (precision casting machines using the vacuum-pressure, vacuum and centrifugal techniques)
• Structural design and strength analysis software (ANSYS, ABAQUS, CATIA, INVENTOR, SOLIDWORKS, MATLAB)
• High-performance computing clusters
• Machine workshop (lathe, milling machine, automatic saw, disc cutter, microtome, drilling machine, sandblasting machine)
Recent research projects of STL
- “Safe and Efficient Marine Transportation of Liquid Hydrogen”, HORIZON-JTI-CLEANH2-2022-02-06, 2023-2027.
- “Digital Ship Structural Health Monitoring – dTHOR”, EDF-2021-NAVAL-R-SSHM, 2022-2025.
- “Safe and efficient storage of ammonia within ships – NH3CRAFT”, HORIZON-CL5-2021-D5-01-07, 2022-2025.
- “Operator-Centered Enhancement of Awareness in Navigation – OCEAN”, HORIZON-CL5-2022-D6-01-08, 2022-2025.
- “Development of multifunctional fiber reinforced composites with nano-modified matrix phase towards wind turbine applications (AIOLOS)”, NSRF, 2021-2023.
- “Design of Dual-fuel Electric Passenger Ships (ELCAT)”, NSRF, 2020-2022.
- “Study of the Adequacy of Advanced Materials for Open Sea Fish Cages – Numerical and Experimental Investigation under Real Loading Conditions (MATISSE)”, NSRF, 2020-2022.
- “Realisation and Demonstration of Advanced Material Solutions for Sustainable and Efficient Ships (RAMSSES)”, funded by the EU, H2020 Programme, 2017-2021 (NTUA Coordinator), http://ramsses-project.eu.
- “Ship Lifecycle Software Solutions (SHIPLYS)”, funded by the EU, H2020 Programme, 2016-2019 (NTUA Coordinator), www.shiplys.com.
- “Design, Manufacturing and Testing of Deep Sea Pressure Housings Made of Composite Materials”, funded by the Greek General Secretariat for Research and Development, 2013-2015 (Project Coordinator).
- “Materials On-board: Steel Advancements and Integrated Composites (MOSAIC)”, funded by the EU, 7th Framework Programme, 2012-2015 (NTUA Coordinator),
- “Filament Wound Composite Pressure Tanks”, funded by the Greek General Secretariat for Research and Development, 2011-2014 (Project Coordinator).
- “Environmentally Friendly Antifouling Technology to Optimise the Energy Efficiency of Ships (FOUL-X-SPEL)”, funded by the EU, FP7 Programme, 2011-2014 (NTUA Coordinator).
- “Composite Patch Repair for Marine and Civil Engineering Infrastructure Applications (Co-Patch)”, funded by the EU, FP7, 2010-2012 (Project Coordinator), http://www.co-patch.com/.
- “Surfacing System for Ship Recovery (SuSy)”, funded by the EU, FP7 Programme, 2010-2012 (NTUA Coordinator).